It happens all the time: A maintenance plan is delayed because a spare part is (apparently) obsolete and nearly impossible to source. The problem isn't just the delay. It's that the maintenance team now knows their risk has increased as the part may be desperately needed to repair the equipment. Worse, doubt begins creeping into the team's thinking. People begin to wonder if this part was obsolete, and we didn't know, what if there are other obsolete parts? The hardest part of this realization is that it is likely that there are, in fact, a lot of obsolete parts in their inventory.
The challenges of managing spare parts have become so commonplace that many accept them as an inevitable aspect of maintenance, repair, and operations (MRO). However, no matter what industry your company operates in, it is possible to manage your spare parts painlessly without sacrificing your team's sanity.
In this article, we'll cover the key drivers of parts obsolescence and offer some strategic insights on how Sparrow can help you navigate this never-ending challenge. Let's get started!
What is parts obsolescence?
Let's start with the basics. Obsolescence is a natural part of the life cycle of almost every component. Components are introduced to the market, sold for a few years, and then reach their "end of life." This happens due to the introduction of new technologies, changes in standards, or changes in regulatory compliance (e.g., IE3 and IE4).
The result? Companies struggle to find the parts they need, when they need them - putting uptime at risk
Why you don't know your inventory parts are obsolete (& what to do about it)
How should this work?
It's not a new problem, either. Machine manufacturers are often responsible for alerting their customers that a component in their equipment is about to become obsolete. But, they actually don't always have the lifecycle data themselves, as we’ll later learn.
However, when machine manufacturers do know that a part is about to become obsolete, they can suggest upgrades or retrofits to the equipment so that their customers can work with newer replacement parts. This is a common practice to improve the overall functionality of the equipment and allow the company to better take advantage of new technological advances as the industry becomes more innovative.
However, most companies don't take advantage of these upgrades. Budget constraints force them to work with what they already have. This includes keeping machines and production lines alive for as long as possible, often resulting in tricky legacy machines that become the cornerstones of factories as new and innovative machines are built around them.
The impact of parts obsolescence
Maintenance managers have a common saying, "when you need it, it’s too late," which really sums up the problem with parts management. It's also why, when a machine breaks down and needs a specific part, it can sometimes be nearly impossible to find.
The result can be problems such as rush orders for parts and extra charges for expedited shipping. Then, until the part arrives, the machine sits idle. That is, of course, if the part can be found in the usual markets at all. In some cases, a maintenance manager has to go to part resellers. This can mean significantly higher prices. All this means machines sit longer than necessary. That reduces productivity and cuts into profits.
This reality of obsolete assets reminds us why we need to think ahead and plan strategies to avoid pitfalls and ensure smooth operations.
You’re not getting enough information
Spare parts obsolescence tends to go unnoticed. That's because there is no standard notification mechanism to alert companies when components are no longer available or supported. Each manufacturer and supplier has its own process when listing parts as obsolete (some even have no process at all). This can get tricky when you have more than 1,500 manufacturers for your spare parts. As a result, there is a high probability that a company will potentially miss out on a notification — if they receive one at all. In addition to missed notifications, companies currently lack the ability to obtain obsolescence data from manufacturers. After all, many parts are purchased through machine builders or parts distributors who don't send obsolescence or upgrade notifications.
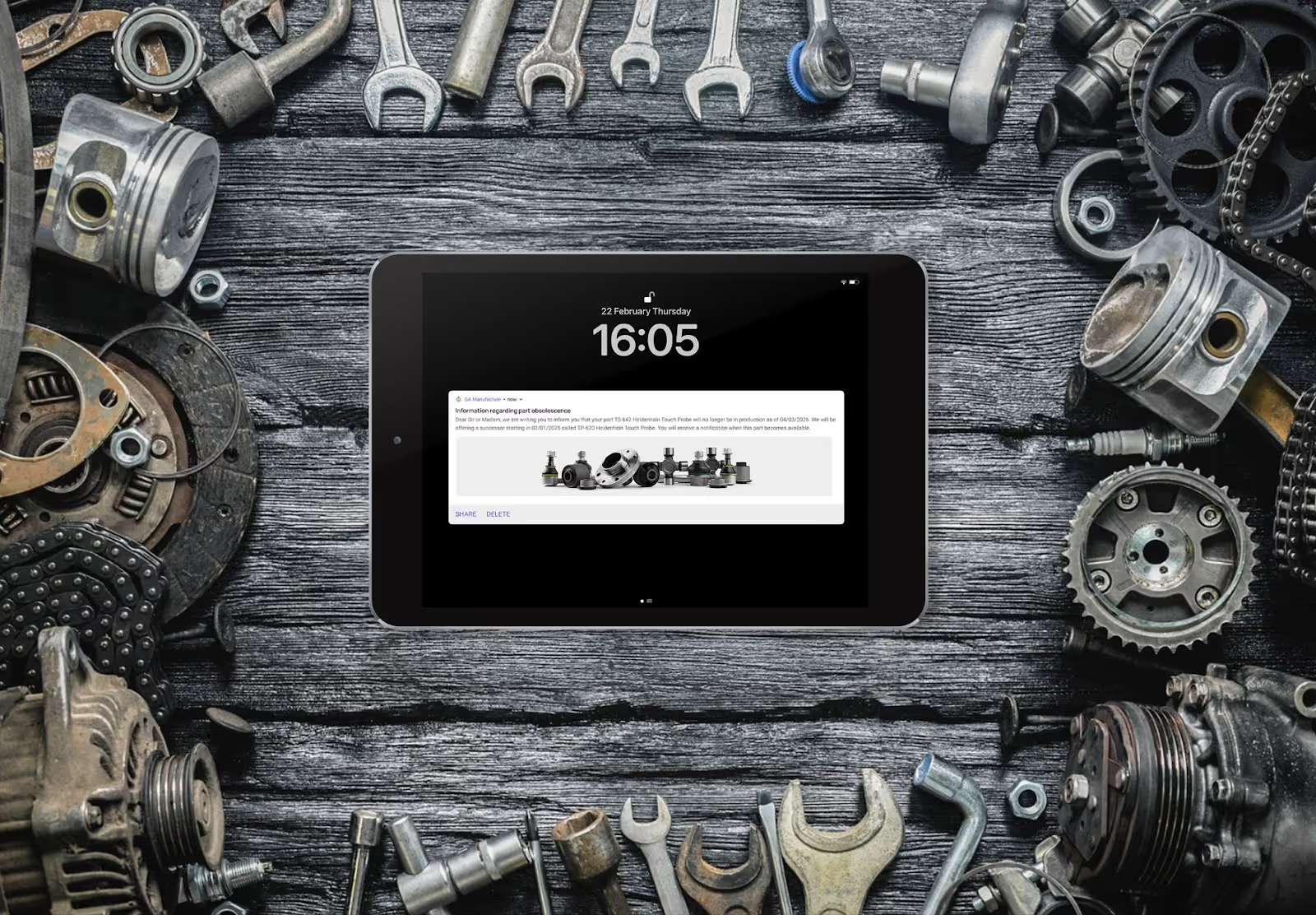
How can we solve this?
Navigating parts obsolescence requires a proactive and informed approach. Addressing the root causes identified earlier boils down to two actionable solutions.
- Get the information: The importance of consolidated, real-time information cannot be overemphasized. Invest in advanced inventory management systems like Sparrow, which sources lifecycle data from manufacturers and suppliers. Such systems can notify you about potential supply chain disruptions, give insights into parts nearing their end of life, and help you understand changing industry trends. Unified data not only empowers you to foresee challenges but also equips you with the knowledge to make informed purchasing decisions.
- Purchase enough parts for your lifecycle: Once you have the right information, the next step is strategic procurement. Instead of making sporadic purchases based on immediate needs, consider the entire lifecycle of your machinery or systems. Estimate the quantity and types of parts you'll need over this lifecycle, factoring in potential disruptions or discontinuations. Gain a long-term view of your parts lifecycle through the use of AI with SPARROW.Plan. We’ll eliminate overstock and reduce downtime without any additional work for your team.
-
Preventing obsolescence using spare parts management software
Now that we've identified the main cause, how do you avoid falling into the obsolescence trap? Enter spare parts inventory management software — specifically Sparrow, which (in our biased opinion) is uniquely tailored to address these challenges. How do we do it?
Real-time inventory visibility
SPARROW.Stock Manager provides real-time insight into inventory status. This enables you to promptly adjust your procurement strategies, minimizing the chances of stockpiling obsolete parts.

Spare parts optimization
SPARROW.Plan offers a unique solution for predicting spare parts needs. Using your data, such as spare parts inventory and BOM lists, combined with manufacturer details and insights into the supply chain, Sparrow provides best-in-class forecasts for spare parts demand.
Spare parts pooling
Forecasting the need for spare parts is challenging: demand is inconsistent, and the time it takes to get these parts is irregular and in flux. That’s why it’s inefficient to make spare parts stocking decisions at a single-site level. The solution? SPARROW.Pool.
By pooling many sites that have similar spare parts needs together, each site can get by with fewer parts in stock and rely on the network when needed. This reduces the risk of overstocking or understocking.
Minimizing parts obsolescence: Supporting practices
Spare parts maintenance and management with Sparrow is a proven way to keep parts obsolescence at bay. You can combine our software with your other maintenance practices to achieve a more efficient and practical overall maintenance strategy.
These are the first steps:
- Regularly audit your data: To maintain the integrity and reliability of your data, data health assessments are essential for any organization. You can think of it as a form of preventive medicine. With the help of a dedicated team or innovative automated tools, you can ensure that your data is always accurate and relevant. The other benefit of conducting periodic assessments is that they help you understand how to improve current data management practices. Here’s a list of our best practices for auditing and cleaning your data.
- Collaborate with vendors: Establish strong communication channels with vendors. They can provide valuable insights into upcoming product changes or phase-outs. Tools like Sparrow.Clean can be used to make this work easier by using machine learning to enrich and clean existing data.
- Train your teams: Ensure that the procurement and inventory management teams are well-versed with the latest industry trends. A well-informed team can make strategic decisions that align with the company's operational needs.
- Recycle or dispose of parts in a timely manner: Have a clear strategy for putting obsolete parts back in the industry ecosystem. Whether it's selling them at discounted rates, recycling, or donating, a plan ensures that obsolete parts don't sit idle in warehouses.
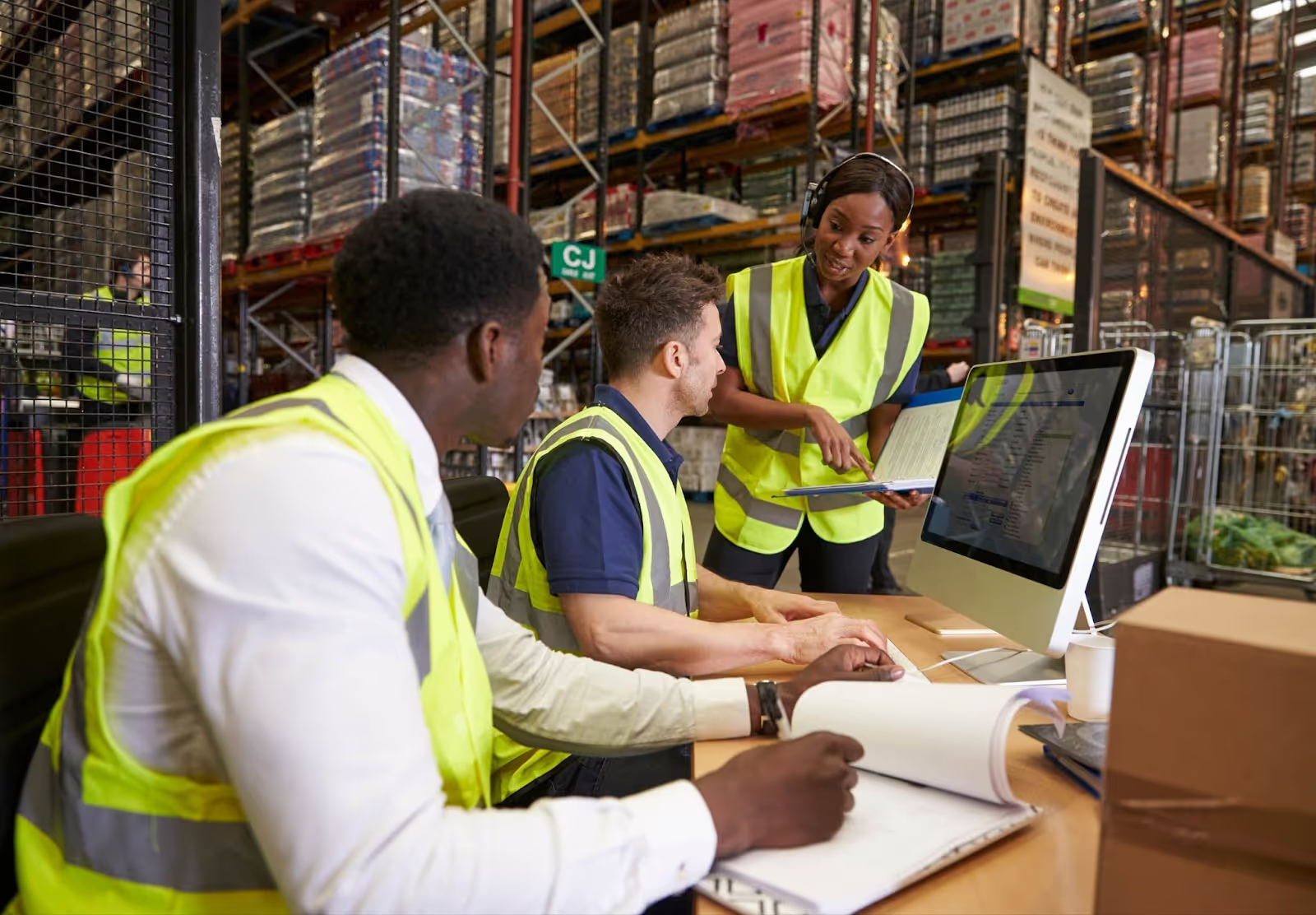
Wrapping Up: How Not to Become Obsolete
Following these steps can help you manage obsolete parts and create an inventory management environment to keep your business running smoothly. With an eye on the future and Sparrow as your parts co-pilot, you can stay ahead of the curve. Ensure that your parts inventory is always optimized and aligned with your operational needs.
Interested in learning more about how Sparrow can help you prevent parts obsolescence? Contact us.