Editor’s Note:
Since first writing this article, little has changed – few companies have adopted a spare parts pooling strategy. At Sparrow, we believe this is low-hanging fruit, a quick-win for firms looking to optimize their manufacturing operations without incurring more costs.
After five years of learned experience, including talking with hundreds of professionals and operating in over 100 plants, we’ve decided to revisit this article with fresh eyes. We’ve rewritten it with a focus on the real issues that manufacturers face, and how spare parts pooling can help mitigate or entirely solve these problems. If we did our job well, this text should serve as a starting point for companies beginning their pooling journey, though even the basic outlines presented here can be implemented to positive results.
Spare parts management is difficult. There’s a tricky balance to be struck between accessing a critical spare part exactly when you need it (to minimize machine downtime) and keeping your inventory value as low as possible (to minimize working capital).
Most firms operate on the very slight probability that they’ll need a specific spare part for a specific machine at any given moment – but it’s a huge challenge to accurately model this exact probability.
One simple-to-implement workaround for this problem is spare parts pooling. From a statistical perspective, predicting when you might need a spare part is difficult with no or little data. By pooling supply and demand across sites (or organizations), you increase your access to both more data and more spare parts. This allows you to forecast more accurately – and source parts more efficiently if the models fail.
Compared to other systems, it’s a fairly simple system to put into place – and pooling is much more cost-effective. Despite that, it’s not implemented as widely as one would think, representing a huge missed opportunity for manufacturers. In this article, we’ll dive into the whys and hows of spare parts pooling!
What is spare parts pooling?
Spare parts pooling is a simple idea at its core: providing access to a shared stock of spare parts to different interested parties. This can be accomplished with an online spare parts “marketplace” system, for example.
Though many firms engage in ad hoc, informal pooling efforts, there are a few different categories of parts pooling:
Internal pooling -
pooling all the spare parts within your company, across all your sites, in one virtual/real store room. This way, anyone who needs a spare part can access one internally at any given moment. Within internal pooling, there are three different options:
One level internal pooling - where all the parts are stocked centrally and issued upon request.
Hub and spoke internal pooling - where most parts are stocked in one location, with some critical items located at various sites.
Network internal pooling - a pool across multiple sites, without a "main" site for stocking.
External pooling -
a pool with external parties outside your company. These may include other similar companies, suppliers of spare parts, or machine manufacturers. Participants in the pool may be either buyers of spare parts or sellers as well. Types of external pooling include:
Cooperative pools - participants know and agree to share resources with each other. For example, the IATP - International Airlines Technical Pool - a pool of over 100 airlines sharing aircraft recovery kits, aircraft parts and tooling, ground handling equipment, and manpower/facilities.
Open pools - members request and share parts anonymously, allowing you to source parts from anyone nearby who has them (even competitors!). Open parts pooling is one of Sparrow’s functionalities, for example.
Pooling: the best way to optimize your spare parts management
The advantages of spare parts pooling
1) Optimized inventory levels
One of the basic advantages of pooling is that it helps you better manage your spare part inventory levels. For most operations, individual part usage is erratic and hard to predict (in the business, they call this kind of demand “lumpy”). To compensate for the unknown demand, companies almost always stock more parts than they’ll ever need – while simultaneously never having enough for unusual situations. The following example illustrates the core of this problem:
Generally speaking, a company can’t know when exactly it will need a part, even with the best predictive models. They may assume they’ll only need a specific part every two years. All of a sudden, a series of malfunctions mean that five parts are needed ASAP. The likelihood that the company has enough of this specific part in the plant(s) where the machines break is very small, leaving them vulnerable to surprises.
To compensate for these eventualities, many firms overstock, buying more than needed all at once. This is expensive and unwieldy, and often doesn’t account for a given part’s usable shelf life. Companies can also run into issues with minimum purchase amount, wherein their need for a part is far lower than the actual sellable quantity, causing them to buy more parts than they likely need.
By opting for a pool-based spare parts management model, you pool the demand between participants. So instead of one company keeping more parts than it needs to minimize downtime, two companies can split the total parts between them and shift them as needed. When scaled up to include all the machines across plants or all the plants in the pool, everyone can stock fewer spare parts. Together, the participants will be closer to the optimal number of parts per the number of machines covered by the pool.
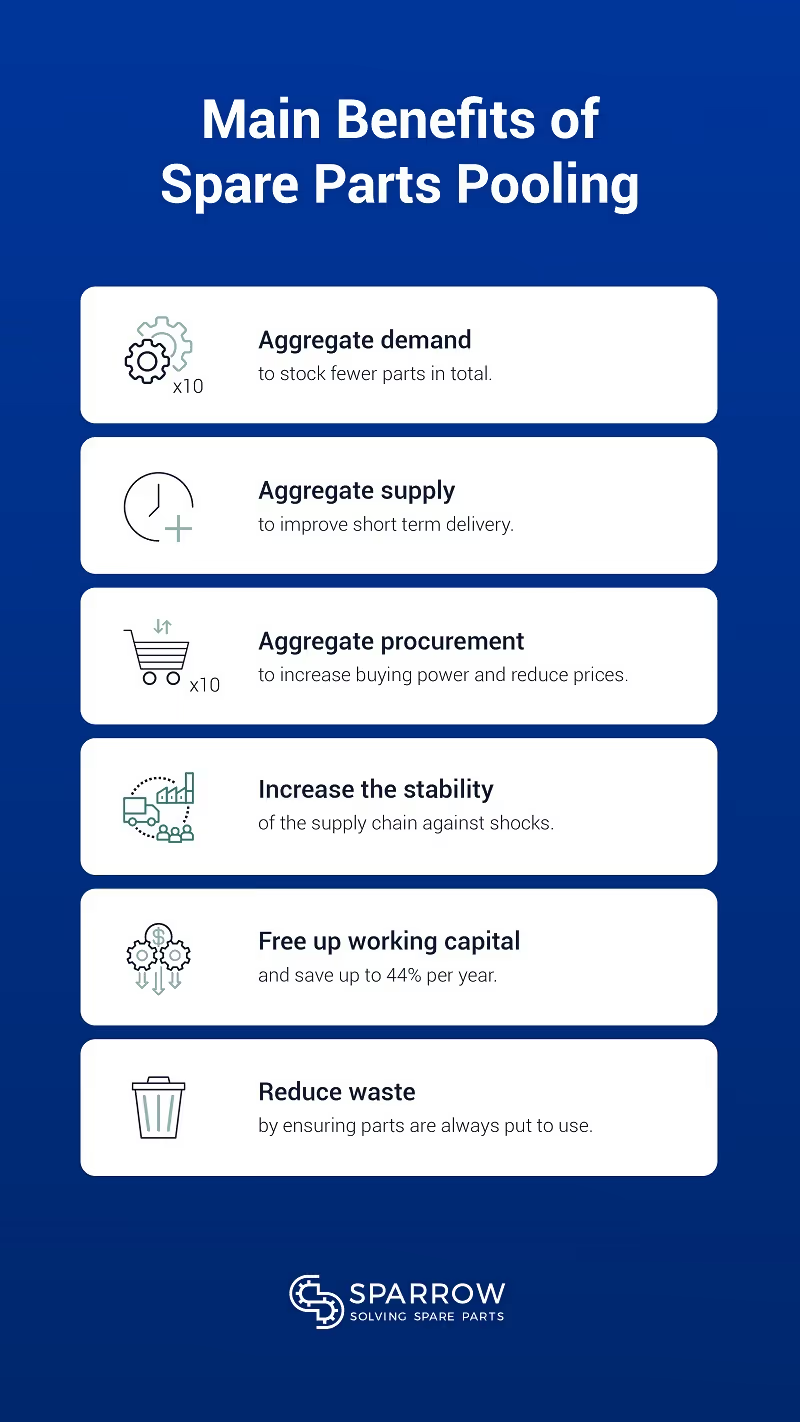
2) Reduced downtime
On the supply-side, pooling helps you cover rare, unforeseeable occurrences. In the spare parts industry, this could be something like needing a second motor when you’re already waiting for one motor of the same kind to arrive (which usually takes weeks or months). The probability of this happening is low, but it’s never zero. Logically, when you have access to more spare parts quicker – via an internal or external pool – you don’t have to fear these events as much. When your spare parts supply is pooled, you can avoid long lead times during an emergency by sourcing parts from either local operations or from a marketplace of suppliers. Spare parts pooling helps maintenance crews react much faster, offering an extra level of security against unplanned downtime.
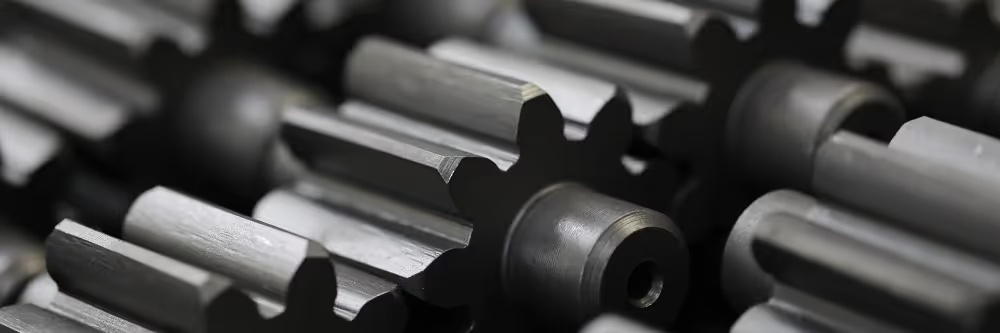
3) More efficient (and cheaper) procurement
Spare parts pooling empowers procurement managers to make smarter, more cost-effective decisions. Typically, procurement teams purchase parts from a small list of producers, and they may pay higher costs to access a spare part from the company they know best. Accessing a wider catalog of parts from a variety of suppliers is time-consuming and research-intensive, making it difficult to prioritize when short-term maintenance needs and the risk of malfunction loom over an operation. Buyers aren’t able to compare prices or leveraging their buyer power.
By engaging in spare parts pooling, procurement departments have more options and control over their supply. Firstly, they may not need to actually purchase anything – the parts might already be in stock at a different location within the organization. If the internal pool can’t provide the part, then pooling as a concept offers procurers access to more data on spare parts availability, location, and demand. The procurement team can then decide on suppliers based on important criteria rather than the customary way of doing things, potentially saving time and money in the process. In the end, spare parts pooling means that procurement is a lot easier – and cheaper – from the buyer side, while suppliers enjoy access to a wider customer base.

4) Higher supply chain resilience
Over the last decade, major supply chain disruptions have become almost commonplace. When the Covid-19 pandemic struck, the importance of supply chain resilience became a major topic. A year later, the ship Ever Given shut down trade through the Suez Canal, teaching the world a lesson on supply chain vulnerabilities. Brexit, conflict in Ukraine, and the flooding of a critical semiconductor supplier are all examples of further show-stopping disruptions.
How does pooling improve supply chain resilience? When the supply chain gets disrupted, having a parts pool in place is like having a top-tier immune system. As a spare parts buyer (machine operator), if suppliers from other places fall through, you still have a back-up chain of local supply and internal stock. Large external pools that cover whole industries (and therefore whole swathes of the supply chain) also make the whole chain more resilient, allowing companies to share resources and plan better to avoid worst-case scenarios. Even without major disruptions, having an internal country pool can mean more stability for countries where external procurement is simply difficult.
5) More working capital
On a basic level, when companies pool parts and aggregate both supply and demand, they increase efficiency drastically. Additionally, optimized inventory levels, less unplanned downtime, and lower overall procurement costs contribute to significant cost savings. For example, a 2014 article by Karsten and Basten suggests that annual savings of 44% may be obtainable via pooling. Our experience and the existing science indicate that spare parts pooling is much more working-capital-effective than operating in silos.
6) Reduced waste
Over the past decades, waste reduction has moved closer and closer to the forefront of global business strategies. Policy shifts (like EU Green Deal) contribute additional incentives – and punishments. Waste-reduction is a byproduct of pooling, as aggregating supply and demand means stocking fewer parts and using those that are stocked more frequently. This, in turn, means that fewer parts become obsolete or get destroyed. The latter might surprise some, but it’s critical to remember that spare parts have a shelf life. Electronics, for example, often become unreliable or unusable after 1-2 years; conveyor belts after 5-7 years. Companies are burning money and resources simply by having too many spare parts on a shelf somewhere. By continuously cycling them, on the other hand, the entire usage of spare parts across the industrial ecosystem is reduced. Put simply: with spare parts pooling, more parts are effectively used; fewer parts are bought and thrown away.
Why aren’t more companies pooling spare parts?
If the advantages of spare parts pooling are so clear, why aren’t more companies adopting this approach? The truth is that most companies face a number of blockers to an efficient pooling strategy. Focusing on internal pools (which should be fairly straightforward), here are several challenges that typically arise:
- Fragmented IT Systems - Many companies operate with multiple ERPs —sometimes up to 200 — and these ERPs are rarely integrated. This lack of connectivity hinders data sharing, even causing some plants to use Excel spreadsheets for parts tracking.
- Data Inconsistencies - A unified spare parts catalog and standardized naming conventions are often missing, making it difficult to locate parts across different sites.
- Local KPIs - Site-specific KPIs for uptime and availability can lead local managers to prioritize their own parts inventories over sharing with other locations, even when nearby plants are in need.
- Logistical and Financial Barriers - Many plants function as independent financial entities, requiring accounting adjustments each time parts are shared. Additionally, transporting parts between locations can introduce logistical challenges, especially at scale.
-
If these challenges are preventing you from establishing an internal parts pool, Sparrow is here to assist.
Pooling: a solution for spare-parts management
Pooling is a no-brainer when it comes to spare parts management. Whether you start small and pool parts internally within your company or you join a wider external pool with several supply chain actors, parts pooling provides access to a common-sense spare parts management method that saves you both money and time. It also makes your operation more resilient, empowering you with spare parts when and where you need them. This strategy doesn’t just benefit single actors in the manufacturing ecosystem; the science demonstrates that pooling is the best option for a more optimized, resilient supply chain too. With disruptions becoming more standard than exception, this is more important than ever.